WEIGHTING: ADVANTAGES AND DISADVANTAGES OF ELECTRONIC BATCH RECORDS
In the past years the documentation effort in the pharmaceutical industry increased tremendously, and the batch records accumulating have grown almost as much as the capacity of some media. As in the meantime more and more manual systems are transferred to electronic systems, for a lot of companies the question now is whether the considerably risen documentation effort can possibly be combined with the enormous increase of hard and software efficiency. With the appropriate electronic system not only the accumulating data can be saved and secured comprehensively but data can also be generated automatically, integrated into the batch record (no more annoying attachments) or even control processes completely. It further allows connections with additional automatic process control and guidance systems and also opens up possibilities of data evaluation. Control systems such as the Management Review or the Product Quality Review, PQR) can be combined with the system. In theory there are practically no limits in system automation.
But how does this present itself in reality? Most of the time additional paper prints are generated (so called hybrid system). And frequently it is quite difficult for long-serving employees to manage major changes in their daily routine. After all, with introducing an electronic system, manufacturing instructions are executed completely electronically and the operator is now being led through the process by the system and not vice versa. As mentioned before, even though the documentation on paper is very time consuming, it is still the result of a grown structure, and the systematics are understood by the staff. Furthermore there are a lot of reservations against complex processes, possible system breakdowns and in general against all unknown.
The advantages for the company are obvious though: a lot of operations and processes can be organised more efficiently and accelerated. Possibilities are shown in the following list:
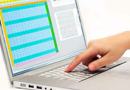
Recommendation
Tuesday, 29 April 2025 13.30 - 18.00 h
Excel in the GxP-regulated Environment - Live Online Training
- Information exchange between the systems
– Quick access to information (e.g. amounts, release status)
– Simultaneous access by different people
– Interfaces with other systems (one-time data entry etc.) - Improved planning and controlling of production processes with better results
– Target and control of the process order
– Integrated equipment administration
– Improvement of the „right the first time“ rate
– Reduction of cycle times and storage costs
– Real-time documentation of process steps - Improvement of process security
– Early detection of deviations
– Reduction of the error rate
– Provision of all data necessary for the evaluation of the batch quality
– Improved data quality in reference to the process and product evaluation
– Improvement possibilities are easier visible - Reduction of administrative efforts with the maintenance of batch records
– Automated generating and clearing of production parameters
– Automated completing and clearing of production instructions and logs
– Reduction of copying activities
– Reduction of review and clearance times - Data processing and integration into other evaluation systems
– PQR
– Trend analysis
– Economic systems
– Deviation management
If used properly, this can lead to a lot of saving possibilities. In a case study presented at the Concept Seminar D3 Electronic Batch Record in Heidelberg this proved to be clearly true. A representative of a Solid Formulation Manufacturer with an annual production volume of about 5000 orders (5-6 billion tablets) reported on the following immediate effects since the introduction of EBR:
- Running times: minus 40%
- Staff requirement: minus 10%
- Service level: 99,9 %
- Error rate in €: minus 70%
- Operating costs for 1000 tablets: minus 33%
There are some issues to be considered for a planned implementation, though. The electronic batch recording is a very complex system with many interfaces on many levels: company-wide planning software, detailed planning systems of the management, process management level, SPS and, of course, connected quality control systems. Therefore, an electronic system cannot be implemented all at once and some changes and special programming of the present system must be done beforehand. In addition high validation efforts and operation and maintenance costs need to be considered - just as well as necessary training activities and possible problems during the implementation and a possible business breakdown. Finally, flexibility will be lost due to the strictly established process regulations.
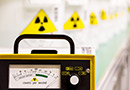
Recommendation
29/30 April 2025
GMP and Quality Requirements for Radiopharmaceuticals - Live Online Training
It is not that easy to measure the cost-benefit relation for existing processes. However, it will change at the latest when introducing new product lines. Then the advantages mostly prevail. If looking at the development of computer-based systems in general it becomes obvious that the electronic batch records have a great future.
Author:
Wolfgang Schmitt
CONCEPT HEIDELBERG