SERIALISATION: WHAT IS THE QUALIFIED PERSON'S (QP) ROLE?
The falsified Medicine Directive was developed in response to growing concern in the market place after discovery of unauthorized sale and supply of counterfeit medicines with potential risks to the patients. The Falsified Medicine Directive (FMD) (Directive 2011/62/ EU) published on 1 July 2011, introduced tougher rules with intention to improve the protection of public health with new harmonized measures ensuring that medicines supplied within the EU territory are safe and the trade in medicines is rigorously controlled. This directive introduced several control measures including obligatory safety features on the outer packaging of the medicines, to be detailed via a delegated act.
The delegated act (Commission Delegated Regulation (EU) 2016/161) detailing the characteristics of the safety features, how medicines authenticity should be verified, and by whom, was published by the European Parliament and the Council, on 9 February 2016.
The delegated Regulation, will apply as of 9 February 2019, in other words pharmaceutical industry is legally obliged to ensure implementation of these regulations on or before 9 February 2019.
Whilst the directive and the delegated act introduced several measures to improve safety of medicines, the current regulatory focus is on the implementation of two key features; tamper evident and the provision of a 2D barcode for verification of authenticity of each unit in the supply chain. These features are expected to ensure legitimate medicines are traded and supplied across the European Union.
With short time remaining for implementation and full compliance with the regulations, very little attention is being paid to inclusion of the tamper evident feature on the packs. This is partly because the tamper evident feature is an old technology and very well known to the pharmaceutical industry. However, all the focus is on the verification and traceability of each single unit to the original manufacturer. In early 2009, various options were evaluated by a group of major pharmaceutical companies supported by EFPIA which resulted in recommendation for use of 2D barcode on individual packs to deliver the regulatory expectations as outlined in the FMD Directive.
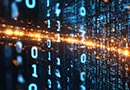
Recommendation
Copenhagen, Denmark26 August 2025
Raw Data - Understanding, Defining and Managing
Whilst the technology for creation, application, reading and verifying the 2D barcodes has been around for many years; used widely in the food industry for example; it is a new challenge for the pharmaceutical industry. Furthermore, the security measures required to ensure data integrity on the single unit throughout the supply chain are very complex, requiring extensive and complicated control systems. Therefore, implementation of the serialisation system for the companies is very challenging which requires design, selection, validation/ qualification of the equipment, software and the process before going live.
So, at a manufacturing site, what activities and systems need to be developed and implemented to enable full compliance?
- Development, design, implementation of the 2D barcodes on all product labels and cartons (as appropriate).
- Changes to the packaging of the products to introduce a 'tamper evident' feature for each pack.
- These changes will require submission of variations and approval of the new labels and packs.
- Application of a temper evident feature on packs and printing a unique barcode on each pack will also require physical changes to the packaging machinery and very possibly addition of new equipment.
- Selection of a suitable vendor, to supply, install and validate the software package to generate unique barcodes, manage rejects, reworks, returns, QA sampling and of course product recall.
- Develop specification, select, purchase, install and validate on-line printing systems, and verification devices to ensure each barcode is printed correctly and is legible at the running speed of the packing machinery.
- Incorporation of the software into the existing site inventory management system, to ensure delivery of the products to the approved customers.
- Introduction of the capability to trace materials in the site warehouse, and the company's supply chain.
- Provision of access to the central database using trained staff to ensure each batch is correctly allocated to the desired market, and make the changes to the database when required. For example, reallocating a batch already in one-member state to another can only take place by the MAH.
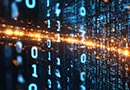
Recommendation
Copenhagen, Denmark27-29 August 2025
Data Integrity Master Class
The Qualified Person (QP) responsible for batch certification for release needs to play a key role in all the tasks listed above. This will include being involved in developing the specifications, defining the validation criteria, and the test protocols to ensure ongoing compliance with the requirements. Management of the changes, management of the deviations and complaints occurring post implementation of the verification codes will be an additional challenge for the QPs. There is no doubt that this is a step change in our operations, where QPs need to be very pro-active and focus on both technical and operational challenges, and where possible apply risk management principles to make decisions and proceed. The QP should also play a key role in preparing the site team and more specifically the QA personnel to handle the issues developing detailed operating procedures and training all involved. There is no doubt there will be few teething problems in early days of implementation, however, with good planning and ongoing monitoring of issues, the benefits of the new process will be realized across the supply chain and for the benefit of the patients as well as the Pharma industry.
Author:
Dr Afshin Hosseiny
... has more than 20 years of experience in the pharmaceutical industry - at first in analytical services, later in quality assurance. Today he is General Manager of Tabriz Consulting and Chairman of the European GDP Association.