GDP MEETS CAPA
Good Distribution Practice (GDP) Guidelines and Good Manufacturing Practice (GMP) Guidelines require organisations to implement effective Corrective Action and Preventive Action (CAPA) systems.
To ensure a CAPA system is implemented and used correctly firstly identify all the steps leading to an event/risk/ issue/non-conformance i.e. identify the 'problem' which requires a solution. Secondly, understand the identified solution must be lasting and must not cause a ripple effect into other business areas. Simply put, the solution mustn't cause another problem elsewhere in the system or organisation, either imminently or in the future.
Prior to an organisation identifying Corrective Action(s) and Preventive Action(s) it is important to work through a systematic investigative process at each link of the chain of events to identify actual or potential "failures" or deviations from the expected norm. And prior to commencing the investigation the definitions used in a CAPA system must be properly understood. See Summary Points.
Proper deviation handling provides a framework for a decision making process based on: (1) Evidence: Document everything known, providing references where available e.g. SOPs, Airway Bill, Copies of shipping documents, temperature printouts. (2) Objectivity: Be open, truthful, concise, clear and accurate. The first step is to accurately detect the event. What is being reported? See Figure 1 for examples.
This 'evidence' is used to both log and trend an event (stop here) or raise a deviation for investigation from e.g. trend analysis, customer complaint.
A Deviation Report (DR) is populated with evidence gathered during deviation handling. At this stage the Deviation Investigator should ask, for example:
- What decisions were made?
- Who made the decisions?
- Did they have authority?
- What information or evidence was used to justify the decision?
- How accurate are written procedures?
Further questions arise:
- Are SOPs clear and accurate with defined lines of responsibility and accountability?
- Why weren't staff trained in specific procedures?
- Why did staff take on responsibilities belonging to another area?
The next step is to log the 'immediate corrective action' taken. Although simple, if not properly documented, it could lead to recurrence of the same event.
The following example DR is generated from a cold chain breach. The reported event is "fridge temperature breached +8°C for 10minutes due to open fridge door". The immediate corrective action is to "close the fridge door", document the excursion and whether product was affected. To prevent recurrence personnel should be reminded to ensure doors are properly closed after entry/exit. This ends the investigation report: if the temperature breach had no impact on product integrity there is no investigation and 'no CAPA'. The person in charge should log periodic checks, trend any findings and assess impact on product (again) and potentially assess operations.
Fig. 2: Deviation Handling and the Typical Investigation Steps taken to reach a Root Cause, considering the risks posed by the problem to resolve and the knock on effect of decisions.
However, the investigation remains open if the event recurred repeatedly or other findings result. The DR investigator should check when the fridge was last serviced, e.g. are there issues with door seals, hinges, gas? A Corrective Action may be to call an engineer. Again, more questions arise (see also methods below):
- Was this issue reported? When? Who to?
- What happened?
- Who made the decisions?
- Whose authority was sought?
- Was any of this documented?
Now the investigation navigates toward identifying Root Cause (RC) and performing Root Cause Analysis (RCA).
Note: properly conducted investigations lead to accurate identification of the RC which in turn lead to appropriate Corrective Actions and where required Preventive Actions. Thus the realisation becomes that CAPA(s) follow through from correctly identified RCs and following a RCA.
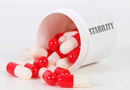
Recommendation
10/11 September 2025
Stability Studies to Support Shipping/Distribution of Pharmaceuticals and Biopharmaceuticals - Live Online Training
In this example, the fridge service and maintenance programme may have lapsed due to driving cost efficiencies, management/personnel changes not appreciating the significance of the maintenance programme, or the Quality Management System not accurately documenting the equipment in use or which equipment required routine maintenance and servicing. Preventive Actions would result to address these findings. See Figure 2 for a summary. To identify and perform appropriate CAPAs, the Deviation must be properly handled. This requires the full support of the team and organisation's management.
In most organisations a Quality Department has prime responsibility for the Deviation and CAPA process. The Investigator has prime responsibility for carrying out a full investigation and pulling a team together.
This department should be monitoring and measuring the process, reporting on its effectiveness and assisting Investigators with the process, as required. This department provides the organisation with the tools it requires, however should not be doing the work associated with every Deviation and CAPA.
A number of tools are available to assist with identifying a RC and performing RCA, some are described below.
1. Fishbone (Ishikawa) Method
The Fishbone Method is used to breakdown information into categories and further into sub-categories; identifying what is available and whether it was a cause for concern in this event. Each category is brainstormed identifying and ruling out causes until RC is reached. The '5-Why's' works well with this method.
2. FMEA - Failure Modes and Effects Analysis
FMEA is a risk assessment tool structured towards finding potential failures within a process or system or design by systematically reviewing and evaluating each known step with regards to severity, occurrence and detection, then orders risks by priority. A failure mode states what may 'fail'. Effects Analysis is the review and analysis of the effects of the failure, and its subsequent consequences.
3. The 5 Why's
Simply put, ask "Why?" enough times until RC is reached. Using this method in conjunction with other tools is very useful during deviation handling (investigation) enabling investigators to learn directly from SMEs. The follow through questions then begin with "How?" "What?" "When?" to seek resolutions to the reported event.
To be effective this method requires a multidisciplinary approach to brainstorm and delve deep as a team.
Fig. 3: This fishbone diagram outlines areas to consider during investigation.
Fig. 4: Temperature Deviation to Cold Chain Shipment: This fishbone diagram delves into each area in further detail
Summary Points
CAPA
- Correction: Fix the existing noncompliance
- Corrective Action: Eliminate the cause of the existing non-compliance / other undesirable situation to prevent its recurrence
- Preventive Action: Eliminate the cause of a potential non-compliance / other undesirable situation to prevent recurrence
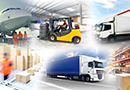
Recommendation
Thursday, 2 October 2025 9 .30 - 16.45 h
Pharma Supply Chain - GDP Requirements and Certification for Logistics Vendors - Live Online Training
RC
- Aims to identify the true cause of an event
- Aims at best to eliminate or at least minimise/control the risk of the event recurring
RCA
- Process for indentifying RC of an event and finding an approach to resolution
- Aimed at reviewing processes and/or systems to prevent events occurring and/or recurring
Deviation Handling
Author:
Prabjeet Dulai
... is Director of GDP & Quality Matters Ltd. Experienced in management and as RP she provides consultancy services and training to the industry covering all aspects of GDP and related GMP areas.