ECA Qualification and Validation Forum
After the publication of version 2.1 of the ECA Good Practice Guide "Qualification and Validation - A guide to effective qualification based on Customer - Supplier Partnership" in 2021, the new version 2.2 was due to follow. It was presented for the first time at the forum.
Authors and users of the guide explained its content and application possibilities to 39 participants from 12 different countries. At the beginning of the event, the current head of the ECA Validation Group, Ralf Gengenbach, gave an overview of the Guide and mentioned the changes to version 2.1.
The aim of the Guide is to outline practical solutions with regard to "lean qualification", to include case studies and to describe prime examples. The guide combines the requirements of Annex 15 of the EU GMP Guide with the FDA Process Validation Guidance and the approach of ASTM Guideline 2500. This approach can be used to address the most common problems in device qualification, see Figure 1.
Figure 1: Challenges in device qualification
Finally, Ralf Gengenbach showed that the ECA Guide is well in line with the ISPE Guide "Commissioning and Qualification" 2nd edition (2019). The ISPE focuses on the process flow, the ECA Guide focuses on the different parties and their tasks involved in the equipment qualification.

Recommendation
30 September / 1 October 2025
Process Validation - Live Online Training
Next, Dr Rainer Gnibl, Government of Upper Bavaria, a European GMP inspector, gave a presentation. Dr. Gnibl explicitly pointed out the flexibility that Annex 15 allows. Especially in the context of FAT, many of these tests can be included in the qualification without having to be explicitly repeated again - if the framework conditions are right. That is, appropriate documentation and a science-based approach as rationale are in place, see Figure 2.
Figure 2: Single performance of tests, checks, reviews...
Rainer Gnibl is also positive about a categorization of equipment to facilitate qualification activities. But a separate presentation on this point followed later. Ralf Gengenbach again took up the topic of Good Engineering Practice and went into it in greater depth.
Ralf Gengenbach sees the great advantages of GEP in the clearly defined "milestones" and the clearly defined workflow. Both lead to precise project plans. Using practical examples, he then showed possible implementations of the most important GEP documents:
• Process documents
• Engineering documents
• Management specifications
• Commissioning documents
Figure 3: Pros (for Live stream FAT)
Figure 4: Cons (for Live stream FAT)
A presentation by Dr Clemens Borkenstein, ZETA GmbH, and Rolf Bauer, Syntegon Technology GmbH, on the subject of remote testing was discussed in great detail. The two speakers - Clemens Borkenstein heads the Remote Testing subgroup of the ECA Validation Group and Rolf Bauer is a member of this subgroup - pointed out that the ECA Guide is the first guide to address the "remote topic" in equipment qualification. They then presented in great detail a checklist of what to look for before, during and after a remote test. They then showed in practical examples, including video animations, how remote tests are carried out at ZETA and Syntegon. The presentation then led into advantages and disadvantages of remote testing, see Figures 3 and 4. Examples of both cases then came from the auditorium. In one case, remote testing went "completely wrong" because the framework conditions were simply not correct. In the other case, testing went smoothly, precisely because of good preparations and different camera positions.
At the end of the day, Jörg Zimmermann from Vetter Pharma-Fertigung GmbH & Co KG and Immediate Past Chair of the International Board of Directors of ISPE picked up on Ralf Gengenbach's statement about the compatibility of the ECA with the ISPE Guide and talked about the current version of the ISPE "Commissioning and Qualification" Guide. He presented the benefits of Revision 2:
- Definition of user requirements including "fitness for use" and differentiation between requirements (what) and specifications (how).
- Distinction between impact on product quality and no impact on product quality.
- Risk assessments to identify Critical Design Elements (CDE's).
- A streamlined Design Review/Design Qualification process with focus on CDE's
- A clear Commissioning and Qualification (C&Q) planning process including a document release matrix
- A lean structure for test execution, including distinctions between engineering and quality aspects, specifying minimum requirements for testing
- The tracebility matrix as a project management tool
- A lean, risk-based "periodic review" approach
- Integration of supplier tests with few test repetitions
- Differences in engineering change management to routine change control
- Current/simple examples of all steps in the Commissioning and Qualification process.
Figure 5: Traditional vs QRM Approach
With the inclusion of quality risk management (QRM), the approach leads to faster market access, as Jörg Zimmermann reported as a result of practical experience at Vetter (Figure 5).
This marked the end of the first day of the conference.
Day two began with a presentation by Maik Guttzeit from Bayer AG. He leads the subgroup on categorization in the ECA Validation Group. Using two examples, a scale and a freeze dryer, he showed the difficulties that supposedly simple devices could show in a categorization. His first conclusion was that there are no simple and clear answers to categorization. He then presented a three-tier categorization model, with the distinction into:
- Non-critical
- Low-critical
- Critical
and supported these categories with examples regarding qualification activities. Maik Guttzeit then showed simplifications regarding DQ and IQ for devices that come "off the shelf" ("commercial off the shelf", COTS). Finally, he gave an outlook on the further development of Annex 9 of the ECA Good Practice Guide, which deals with categorization. It is planned to present different approaches on how to do:
- A matrix approach with a traffic light system (red, yellow, green), see Figure 6.
- A decision tree approach
- A tabular approach
His conclusion was: Categorisation can help to reduce qualification effort - but should never reduce quality.
Figure 6: Categorization - Matrix Approach
Holger Frey from Merck in Darmstadt then presented a case study of supplier involvement in a qualification project. The project involved the replacement of an optical inspection line for vials with integrated leak testing. The project had a value of more than 3 million euros and was planned for a period of 2 years. Documentation from the supplier was also very intensively involved in the project:
- FMEA
- Pre-FAT and FAT I and II
- IQ, OQ
In fact, the involvement of the supplier already started with the requirements specification, see Figure 7.
Figure 7: Qualification Project - procedure qualification project
Interestingly, environmental, health and safety (EHS) aspects were integrated into the user requirements, but as non-GMP-relevant. Thus, they were also not test relevant in the qualification. Especially in time-critical project phases, the FAT activities were integrated into the qualification to avoid duplicate testing. The procedure was carried out in accordance with an SOP and was coordinated with quality assurance, see Figure 8.
Figure 8: Qualification Project- qualification steps
Igor Krasula from Valicare, member of the subgroup "electronic documentation" of the ECA Validation Group, then presented the content of the revised chapter on electronic documentation and gave further tips on how to deal with electronic documentation systems in the context of qualification and validation. This topic also met with great interest. As advantages of electronic documentation he mentioned among others:
- Better readability of reports and easier translation options, if required
- Improved data integrity
- Easier sharing of documents (e.g., to obtain approvals)
- Faster documenting and more consistent terms (when using standard terms)
- Electronic approvals (e.g., via electronic signatures)
- Direct integration of test data (from the equipment itself, from cameras, control panel printouts, etc.)
- Simpler and cheaper archiving
He then went on to discuss a "traditional approach (scanning paper documentation) and an "advanced approach." In this "advanced approach", qualification/validation documents are generated electronically, the tests are entered there, and the whole package is released electronically, see Figure 9.
Figure 9: Advanced Approach
It was very important to him that electronic systems fulfill the data integrity aspects according to the ALCOA+ and ALCOA++ principles. Mr. Krasula expects it to take 1.5 - 2 years until such a system is implemented and can be used. A survey in the auditorium showed that this period is absolutely realistic. The highlight was the live presentation of such a system. It became clear in a very impressive way that sources of error due to incorrect entries can be prevented by appropriate programming of the fields to be filled in.
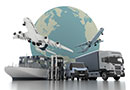
Recommendation
Thursday, 9 October 2025 9 .00 - 12.30 h
Temperature-Sensitive Pharmaceuticals – Transport and Vehicle Qualification - Live Online Training
Axel Heueis, from Drees und Sommer, then took the participants into a somewhat different world, the world of construction, with "3C Management". "3C" stands for Construction-Commissioning- Compliance. It was about construction projects in which GMP requirements (compliance) are integrated in good time from the outset during planning and construction and then during technical testing (commissioning). Mr. Heueis asked the rhetorical question, when should GMP be started in a construction project? His answer was quite simple: the moment the project starts! He then presented a very impressive example regarding concaves between floor and wall in the context of the construction of a cleanroom, which were realized via Pharma-Terrazzo. However, this meant that the freedom to flexibly position cleanroom walls was lost. In order to clarify such coordination issues at an early stage, appropriate project management is necessary, with the corresponding (GMP) interfaces, see Figure 10.
Figure 10: GMP Documents Interfaces and Responsibilities
Finally, Ralf Gengenbach once again presented what he considers to be the six most important errors in a device qualification:
1. GMP and GEP activities are not well combined with each other
2. user requirements are mixed with technical specification
3. risk assessments are not used efficiently
4. integration of suppliers is not well solved
5. FAT, SAT are not used to a sufficient extent
6. GEP is not well established
In explaining point 6, he contrasted testing with qualification. In his sense, it means that qualification is not testing. Qualification is just testing. If one tests during qualification, this can lead to technical defects then having to be corrected during qualification. This in turn leads to increased costs, see Figure 11.
Figure 11: Missing GEP increases the costs and time delay
Conclusion: The new ECA Good Practice Guide "Qualification and Validation - A guide to effective qualification based on Customer - Supplier Partnership" was very well received in the new version 2.2. Many discussions, also at the social event in the old town of Heidelberg, showed the advantages of a face-to-face event. One wish for improvement was to make the guide also available in a simple edition, for (still) less experienced suppliers in the GMP environment. The ECA Validation Group will work on this in the next step.
The guide is available free of charge for members of the validation group, see www.validation-group.org.
About the Author
Sven Pommeranz
... is Operations Director and organises and conducts courses and conferences on behalf of the ECA Academy in the area validation.