Cross-contamination and Sustainability: The Trouble with Contamination
The topic of cross-contamination and its prevention is becoming increasingly important in government audits. Not only the measures taken to prevent cross-contamination are explicitly inquired about, but also how the success of these measures is tested in surface sampling. At the same time, production plants face the major challenge of sustainability, which contrasts with the increased energy and material requirements for prevention measures.
Cross-contamination, according to the glossary of the EU GMP Guidelines1, is contamination of a starting material or product with another material or product. This can occur through the uncontrolled release of particles, gases, aerosols or organisms, as well as through residues on work clothing or equipment, for example due to inadequate cleaning.
Various technical and organizational measures are suggested to prevent the occurrence of cross-contamination. These include physical separation, for example by producing solids in one building and sterile liquids in another. There is also the option of separation within a building, for example by producing products of different risk categories in assigned areas and/or with assigned equipment. Other options are the campaign mode, in which several batches of the same product are produced one after the other with only dry cleaning in between, and the establishment of airlock systems for personnel, equipment or materials. Roughly summarized, the following six areas can be identified to build a "CroCo" risk analysis. It is not possible to subdivide this into "technical" and "organizational" measures the same way the GMP Guidelines, Section 5.21, do, since both types of measures play a role in all of the six areas.
However, with the emerging topic of "sustainability," new questions and problems arise regarding the avoidance of cross-contamination. Specifically, sustainability is about avoiding energy, carbon dioxide, waste, and the use of cleaning agents. The latter should be used as sparingly as possible and also have good biodegradability.
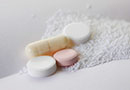
Recommendation
14-16 October 2025
Granulation & Tableting - Live Online Training
Fig. 1: Possible structure of a risk analysis for cross-contamination.
If the six areas mentioned above are evaluated further in detail, many material- and energy-intensive measures emerge. These include the establishment of exhaust systems directly at the production sites to collect any particles that emerge. Material-intensive protective clothing concepts are designed to prevent residues on the work clothing from being transferred to the product. This includes the continuous replacement of GMP clothing in the changing rooms, but also the use of special protective clothing that must be pulled over the GMP protective clothing when entering special production areas. In addition, there is the use of gloves, hard hats and special beard covers. Another important focus is on cleaning: the most critical issue is cross-contamination between different products. Before changing from a batch of one product to a batch of another product in a production area, wet cleaning must be performed according to specified cleaning procedures to remove residues in the area and on the equipment. For this purpose, considerable quantities of cleaning agents and disinfectants are sometimes used and discharged into the wastewater. Another major energy drain relates to ventilation systems. Did you know that up to 90% of the energy demand in a pharmaceutical building is caused by ventilation systems? But this also depends on the mode of operation. By extracting more air in a production room in a solida operation than air is introduced into the adjacent corridor, an air gradient is created in the production room, a differential pressure. This air gradient keeps any particles that may occur in the production room and prevents any contamination of the adjacent corridor or even other production rooms ("clean corridor concept"). In addition, an effective monitoring system must be set up to constantly monitor the differential pressures and generate appropriate alarms in the event of a drop below predefined limits.
Many of the measures listed above partly require a high input of energy, but also of materials. The challenge for the pharmaceutical entrepreneur in the future will be to find a good balance between "cross contamination risk", "use of materials and cleaning agents" and "energy requirements of the plant". We would like to share some ideas with you below.
1. Materials
With regard to "avoidance of materials", the focus is less on the raw and auxiliary materials used in manufacturing, but rather on all materials that are otherwise required for production in general. Disposable or reusable clothing, the above-mentioned "special protective clothing", sampling materials, packaging, single-use equipment, but also paper for documentation purposes are of interest here. In many cases, the question "single-use vs. reusable" now arises. This cannot be answered in a general way, because cleaning also costs resources. You can use the carbon footprint to evaluate all your processes and materials (e.g., in accordance with ISO 140672). It is important that you correctly define the "scope" for your assessment. As a rule of thumb, the more often you can reuse a reusable item, the better the result for the reusable item.
2. Buildings
Quite essential in terms of cross-contamination and sustainability is the ventilation concept. High air exchange rates in a room do ensure a short recovery time and thus faster removal of particles and other contaminants. However, this is countered by significantly higher energy requirements. How far can you safely reduce your air exchange rates? Another possible solution, depending on the building design, could be to drastically reduce the outside air portion of the ventilation. This way, you can maintain strong circulation within the building, but not lose the enthalpy expended. Of course, this requires an appropriate design of the ventilation system. Degree of automation of the ventilation, HEPA filters in the supply and/or exhaust air, exhaust air connections at the bottom of the room, frequency-directed fans, and heat recovery are the issues that must be considered. However, the possibilities and discussion points for a ventilation system do not end there. Adiabatic humidification of supply or exhaust air (in this case for heat recovery purposes), solar-powered reheaters or geothermal energy are further topics to get even closer to "enlightenment" in terms of sustainability. Last but not least, you can think about the real requirements of your humidity in operation. Above all, however, the latter points must always be considered from the point of view of hygiene and microbiological load. For sterile operations, this issue is thus even more critical. Here, the risk analysis for cross-contamination does not focus on particles in the first place, but on microbiology.
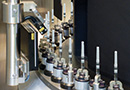
Recommendation
Vienna, Austria21-23 October 2025
Visual Inspection of Parenterals PLUS Pre-Course Fundamentals of Visual Inspection
3. Cleaning and disinfection agents:
Cleaning and disinfection is a central element of the aforementioned risk analysis. The new sustainability requirements will aim to run cleaning processes at lower temperatures (e.g. CIP/WIP). In addition, the quantities of cleaning agents and disinfectants should be reduced as much as possible, and ideally, readily degradable substances should be used for cleaning/disinfection. Chlorine and fluorine compounds, for example, have poor biodegradability. However, the degradability is offset by the efficacy and concentration of the detergents and disinfectants mentioned, which affects the evaluation in the risk analysis for cross-contamination. Incidentally, the same applies to sterilization processes, where the assessment is even more difficult.
Summary
Sustainability and the changes that come with it are finding their way into pharmaceutical operations more and more. However, it can be observed that QA representatives as well as the regulatory side rightly demand a minimum level of control, hygiene and prevention of contamination in GMP operations. This can lead to conflicts. Who will be proven right? How can pharmaceutical processes be made more sustainable without having to forego the previous safeguarding of processes and the corresponding control? Here, representatives of quality and the environment will have to agree on compromises. The key lies in good control strategies and holistic assessment of all risks. Perhaps we in GMP will also eventually find our way to "integrated management systems" that consider quality, environment, safety and health together under one roof?
About the Authors:
Dr Felix Kern is a pharmacist and Head of Compliance Launch and Technology Center at Merck KGaA in Darmstadt.
Fritz Röder is Site Account Engineer at Merck KGaA, Darmstadt.
Source:
1 https://www.bundesgesundheitsministerium.de/gmp.html, retrieved 04.02.22
2 https://www.beuth.de/de/norm/din-en-iso-14067/289443505, retrieved on 04.02.2022