CONTI MANUFACTURING - THE CONTINUOUS MANUFACTURE OF TABLETS
Continuous processes are used frequently for the manufacture of chemicals or food. As these facilities can be constructed in a very compact way and, furthermore, guarantee a fast lead time thanks to the integration of many single steps, the costs of production are usually significantly lower than in the case of batch production.
But for decades the only common procedure for the pharmaceutical production was production in batch processes. Even though single continuous processes such as extrusion, tableting and packaging were used, these usually were not integrated. Instead they were charged from a container with a fixed size and loaded again into such a container.
The world is changing
For about 15 years now a clear interest in continuous manufacturing processes can be observed - especially in the area of solid dosage forms. Multinational firms have been the pioneers in this sector. In the beginning AZ and GSK had the idea to dose all components of the formulation for a tablet in a premixed form from a container into a continuously working facility. In this facility all necessary steps are carried out in an integrated and fully automated way: from wet granulation and drying, the addition of an external phase to tableting. The renowned IChem Award 2012 was awarded to GSK for its realisation of such a facility. Novartis, in contrast, entered into a partnership with the MIT worth many million dollars. The idea is to carry out all process steps from the synthesis of the active pharmaceutical ingredients to the finished tablets continuously.
Reasons
There are many reasons for this increasing interest. First of all it offers the possibility to reduce the production costs. Because of the high level of integration continuously working facilities need considerably less GMP area. This effect is even increased by the fact that semi-finished products need not be put in containers in interim storage in the production environment any longer. This goes hand in hand with a significant reduction of lead times. Authorities, and especially the FDA, have required an improved process understanding and, associated therewith, less OSS batches with the risk of drug shortages for years. Thanks to the progress made in online analytics coupled with a consistent risk analysis it is possible to monitor all critical process parameters in real time today. Furthermore, by using continuous processes it is possible to discharge small amounts of product being outside the specified tolerances and take corrective action by means of an adjustment of process parameters.
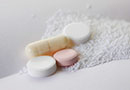
Recommendation
14-16 October 2025
Granulation & Tableting - Live Online Training
This principle has been used successfully in the pressing of tablets for decades. This means that in the case of deviations only small amounts have to be rejected and that only tablets with an acceptable weight can actually reach the market.
Additionally, the importance of a high yield of the processes is constantly increasing because of the trend towards expensive active pharmaceutical ingredients and smaller patient collectives. If single tablets are sold for several 100 Euros, only a few million tablets have to be produced per year even for blockbusters (products with a turnover exceeding 1 billion USD per year). Continuous manufacturing eliminates the need for scale up since clinical samples can be manufactured in such a way that the production facility is used only for a few minutes. And as the production of numerous complete small-batches for the development and optimisation of processes is no longer required significantly less material is needed for the development when active pharmaceutical ingredients are especially rare and disproportionately expensive.
By means of a full instrumentation of the complete process chain it is furthermore possible to realise real time release so that no material is needed for a destructive release testing.
Status Quo
Nearly all multinational pharmaceutical companies have invested now in the continuous manufacturing of tablets. The following are some examples: Janssen Pharma / J&J has constructed a continuous production line for Prezista in Gurabo (Puerto Rico). Previously, Prezista had been produced in batch processes. Now Janssen Pharma has successfully obtained a new registration from FDA and EMA for the continuous manufacture of the product. Additionally, Janssen Pharma operates several continuous facilities of different sizes at different sites. These facilities are used for the development of new products or for clinical trials. In the long run Janssen Pharma plans to develop all new tablets exclusively for continuous manufacturing.
With its PCMM concept Pfizer has decided to take another approach. A complete continuous production line with a nominal capacity of 25 kg/h together with HVAC technology, air locks for material and employees and the complete media supply is placed in 5 transportable containers. These containers can be shipped worldwide on trucks or ships. It only takes a few days to assemble the parts to a fully functioning plant for the manufacture of tablets. Pfizer and GSK announced in 2016 that they will be working on a common standard for this concept. The concept has been awarded with the renowned FOYA Award (Facility Of The Year) from ISPE in 2016.
Vertex from Boston is probably the most prominent example for the continuous manufacture of tablets at the moment. The facility for the continuous manufacture of a medicinal product against cystic fibrosis processes the starting materials to coated tablets within 90 minutes. No following batch release is required thanks to the integrated parametrical release. Approval by FDA took place in 2015 and by EMA in 2017.
Aesoca and Hovione are two contract manufacturers which offer continuous manufacturing of tablets as CMOs. Interested companies thus are offered the possibility to produce clinical samples for new products without having to invest themselves already in this early phase. In a later development phase companies can bridge the time until the delivery and commissioning of their own facility.
Technological turning point
If high-volume products in the amount of several billion tablets per year are produced, low costs for the raw materials are of vital importance. In most cases it makes economic sense to optimise inexpensive excipients with inadequate physical properties by means of wet granulation for the use on high-speed tablet presses. Moreover, the risk of segregation during tableting is minimised by carrying out wet granulation. If a much smaller amount of tablets is required direct compression might be an alternative. Then relatively expensive raw material qualities with a good flowability must be used. But then the step of wet granulation can be omitted. Continuous manufacturing furthermore minimises the risk for segregation as the mixture takes place only just before tableting. Pharmaceutical companies pursue this strategy especially for expensive low-volume products.
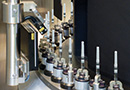
Recommendation
Vienna, Austria21-23 October 2025
Visual Inspection of Parenterals PLUS Pre-Course Fundamentals of Visual Inspection
Summary and outlook
While in the beginning, this technology was offered to interested pharmaceutical companies only by very few equipment manufacturers this has changed now. At the latest since Interpack 2017 all important equipment manufacturers offer continuous manufacturing.
As a number of products is in the clinical trial phase an increasing number of marketing authorisations can be expected for the next years. Generics manufacturers are also increasingly interested in this technology, their target rather being high-volume products.
FDA, ASTM and some consortia of university are working on first standards and guidelines.
Author:
Dr Harald Stahl
... is Group Director Application & Strategy Management within GEA and as such responsible for the comparison and the integration of various technologies as well as for the evaluation of new technologies.