CHALLENGE FOR THE QP: THE CHINESE MARKET
The increasing globalisation and the new legislation in terms of Good Distribution Practices (GDP) pose new challenges for companies in the pharmaceutical industry - a subject that was also part of the discussions of the European QP Association's past QP Forum.
In one of the parallel sessions, it was discussed what challenges a Qualified Person (QP) might face when working with companies based in China and how these might be solved. Of course, there are clear economic advantages (cost savings, large pool of APIs). On the other hand, reliability and quality of Chinese API manufacturers are very heterogeneous. From the experience made by QPs and GMP Auditors it can be concluded that the average compliance level is lower than at western manufacturing sites. It also seems that qualifying a Chinese supplier might need a different risk management process. It became obvious in the sessions that all QPs are struggling with these facts.
If companies rely on common standardised procedures and qualify the new Chinese source quickly, they might get a nasty surprise. On the other side, if they are too worried about what can go wrong, they may miss out a great savings opportunity.
In the past many companies relied on trading companies to take care of the Chinese manufacturers, but the new EU directives, such as the 2011/62/EU amending the 2001/83 directive, requires a more active participation of the QP of the market authorization holder.
A common scenario?
Up to two or three auditors (and sometimes the QP) fly to China to audit the plant. After an exhausting day with temperatures reaching 40°C in the workshop, the audit report is written with five major observations and 20 minors.
Within two weeks a nice response is coming and it turns out that half of the audit observations were a misunderstanding due to a poor translation. The other observations, the manufacturer promises, would be solved as soon as possible. There is often no way in flying back there soon enough to verify everything. And so the supplier is approved.
After two years an EU authority visits the plant and finds several critical issues - the CEPs are withdrawn and the material already on the market has to be recalled. Of course this is a worst case scenario, but there are ways to prevent this from happening.
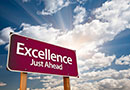
Recommendation
Berlin, Germany9/10 April 2025
KPIs and Quality Metrics
Good CAPAs
It is imperative that the closing meetings are very detailed, to make sure that major or critical observations are well understood.
Too often we take for granted that a CA PA generated after an audit, is fully implemented. But what should be kept in mind is the fact that many plants receive two or more audits every week. And some auditors request unreasonable changes or improvements, which actually contradict other auditors' findings. Further, many companies are too shy to tell the customer that they do not agree with the findings. Another issue is that some companies simply do not understand the observations. They rather merely describe the actions only on paper than really implementing it, because it would change the whole system or, last but not least, it simply might be too difficult or costly to implement the process. As a result, the QP should work together very closely with the Chinese company to find a way to implement the CAPA in a reasonable way and to verify its proper implementation through follow-up audits or visits.
A good translator and clear communication
Another barrier is the language. Often companies are chosen, because the communication is easy. However, in the long run the decision may be commercially (and from a quality perspective) a wrong one. If the QP or Quality assurance (QA) is involved from the beginning, then also a partner can be chosen that may seem to be challenging in the beginning, but might become a trustworthy and reliable supplier later.A regular visit plan
It is expected that audits are conducted every three years. This is probably the only workable time interval for many companies. But is this sufficient? And how can companies get the best out of a commercial relationship without spending too much time on airplanes and on travelling?
Chinese plants compared to EU plants have similar observations, but the number of observations is often larger in China than in the EU. That also means that spot checks are not sufficient. All parts of the plant and documentation must be checked. A one day audit is not enough. It is recommended to spend at least two to three days in the plant. At the end the relevant people in QA have to build up a personal relationship with the corresponding QA staff in the Chinese plant. if the initial suspicion and lack of trust can be overcome, a very healthy and productive relationship can be formed, in which everyone will greatly benefit.
Normally the line of communication is between the purchasing staff and the sales staff of the chinese plants. This also unfortunately often includes communication on Qa matters. It is highly recommended that QA communicates directly with the corresponding QA staff of the Chinese plant. This also applies when trading companies in between are used. The trading company can easily handle the commercial aspect of the relationship, but QA should always have a direct line to the QA of the plant in China.
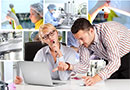
Recommendation
Hamburg, Germany29/30 April 2025
Efficient Batch Record Design and Review
The savings may not be as high as simply the price difference between the EU supplier and the Chinese company, but even when the additional QA costs are added, the savings still can be substantial. The additional investment by QA is worthwhile in the long run, as it can ensure that the plant is fully GMP compliant and no nasty surprises of CEP withdrawals or failed EU inspections occur - and last but not least it will ensure that everyone can have a sound sleep at night.
Author:
York Moeller, J.A. Moeller*
York Moeller, J.a. Moeller Gmbh & co. kG, Germany and china, is currently located in china to support European and us companies to deal with government authorities, plants and distributors in china.
& Wolfgang Schmitt
CONCEPT HEIDELBERG